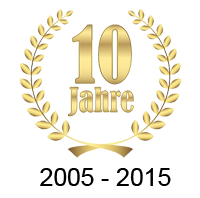
Keramik stammt von dem griechischen Wort „Keramos“ (zu Deutsch „Ton“) ab. Die ersten das Material verarbeitenden Industrien waren im römischen Reich zu finden: Rote, glasierte Gebrauchskeramik, so genannte Terra Sigillata, war rund um das Mittelmeer verbreitet. Die typischen roten Dachziegel sind ebenfalls bereits in großen Mengen hergestellt worden. Auch Bodenziegel wurden in den Häusern eingesetzt. Die römischen Fußbodenheizungen basierten auf keramischen und somit hitzebeständigen Materialien. Bereits 4000 v. Chr. war das Glasieren von Keramik bekannt.
Keramikfliesen als Wandbelag haben sich vor allem in islamischen Ländern einen guten Ruf aufbauen können. Von den Mauren wurden farbig glasierte Fliesen in Spanien und Portugal eingeführt. In Deutschland selbst waren die Fliesen nicht verbreitet, erste Produktionen wurden im Hochmittelalter aufgenommen – konnten sich jedoch nicht spürbar etablieren. Erst mit dem Beginn der frühen Neuzeit entstanden Zentren der Keramikherstellung in Europa, dessen Produkte nach Deutschland exportiert wurden.
Auch heute noch ist Ton für die Keramikfliese der Grundstoff, die Herstellung läuft jedoch maschinell und die Fliese als Massenware vom Band. In der modernen Herstellung werden das Strangpressverfahren und die Pulverpressung bzw. Trockenpressung angewendet. Beim Strangpressen wird aus einer plastischen Keramikmasse ein endloses Band geformt und anschließend in Fliesengröße zerteilt. Im Trockenpressverfahren wird speziell aufbereitetes Keramikpulver mit hohem Druck in Formen gepresst und danach gebrannt. Das Herstellungsverfahren entscheidet unter anderem darüber, welche Qualität die Fliesen haben beziehungsweise in welchem Maße sie Wasser aufnehmen können. Die Farben der Fliesen entstehen durch die jeweilige Energiezufuhr beim Brand. Die unterschiedlichen Elemente in der Mischung werden deshalb erst durch den erfolgten Brand sichtbar.Es werden verschiedene Arten der Keramik unterschieden:
Steingut
Trocken gepresste keramische Fliesen, deren „Scherben“ nach dem Brand bei etwa 950 bis 1100 °C eine Wasseraufnahme von mehr als 10 Gewichtsprozent aufweisen, wird als Steingut bezeichnet. Es ist nicht frostfest, daher wird es ausschließlich im Innenbereich verbaut. Nach der Formgebung des Materials wird heutzutage flüssige Glasur aufgespritzt. Mit siebdruckähnlichen Verfahren können die Fliesen entsprechende Muster bekommen. Die Form ist nicht nur auf die typische flache Fliese begrenzt. So sind durchaus auch Seifenschalen, Handtuchhalter möglich. Diese werden allerdings in Gipsformen gegossen und nicht gepresst.
- Steinzeug
Im Gegensatz zum Steingut wird Steinzeug mit bis zu 1300 °C gebrannt. Durch Zugabe von Feldspaten werden Zwischenräume des Materials quasi „aufgefüllt“. Dadurch erreicht man durch eine höhere Dichte eine geringere Wasseraufnahme von höchsten drei Gewichtsprozenten und bessere mechanische Festigkeit. Steinzeug ist zudem frostbeständig. Die Farbe kann ein- oder mehrfarbig sein. Besonders in stark beanspruchten Anwendungsbereichen - etwa in Industrie, Gewerbe oder öffentlichen Bereichen - sind die Fußbodenfliesen aus Steinzeug beliebt. Die Empfindlichkeit gegenüber Flecken wird durch transparente Glasuren oder werkseitige Oberflächenvergütungen vermindert.
- Feinsteinzeug
Feinsteinzeug wird hergestellt, indem extrem feines Mineralpulver mit hohen Anteilen an Quarz, Feldspaten und anderen Flussmitteln unter hohem Druck trocken gepresst wird. Das Produkt, das in Größen bis zu 60 mal 60 Zentimeter hergestellt wird, hat eine sehr niedrige Wasseraufnahme von 0,05 Massenprozent. Die Brenntemperatur von etwa 1200 °C trägt zu einer sehr dichten Verbindung bei, die bei dem fertigen Feinsteinzeug zu einer hohen Verschleißfestigkeit und chemischen Beständigkeit führt. Die Fliesen werden - vor allem wegen ihrer sehr guten physikalischen Eigenschaften und dem breiten Angebot an unterschiedlichsten Optiken - in vielen Anwendungsgebieten eingesetzt und müssen mit diamantbestückten Nassschneidegeräten bearbeitet werden. Allerdings muss man aufpassen: Normaler Zementmörtel kann beim Verlegen nicht verwendet werden - spezielle Fliesenkleber (Dünnbettmörtel) sind notwendig. Feinsteinzeug eignet sich auch zur Imitation von Natursteinen.
- Cotto oder Terrakotta
Basismaterial für Terrakotta-Fliesen ist Kalkmergel mit starken Verunreinigungen aus Quarzkrümeln, auch „toskanischer Schieferton“ genannt. Der Ton wird mit Wasser vermengt und wie Teig geknetet – an dieser Stelle ist es auch möglich, dass Muster und Reliefs in den „frischen“ Ton eingearbeitet werden. Stahlbürsten erzeugen die raue Oberfläche nach dem Press- und Trocknungsvorgang. Bei einer Temperatur von 950 bis 1050 °C wird Terrakotta nach dem Trocknen dann in einem Ofen bis zu 48 Stunden lang gebrannt. Dabei wird aus dem blaugrauen Ton durch Oxidation der typisch rötlich gefärbte Cotto.
- Klinker und Spaltklinker
Zu den so genannten grobkeramischen Produkten gehören die Klinker. Sie werden als Teig angerührt und im Strangpressverfahren geformt – damit ähneln sie dem Verfahren der Terracottaherstellung. Anschließend kommen die Hartziegel glasiert oder unglasiert bei rund 1200 °C in den Ofen. Das fertige Produkt ist ein idealer Boden- und Wandbelag für Außenbereiche, denn hohe Kantenschärfe und Beständigkeit gegen Wasser und Frost zeichnen den Klinkerstein aus. Spaltklinker heißen so, weil sie als stranggepresste Klinker aus dem Ofen kommen und erst nach dem Brand gespalten werden. Wer genau hinschaut, kann auf der Rückseite die Rillen der Pressung erkennen.
Die Keramikfliesen sind je nach ihrer Fähigkeit Wasser aufzunehmen klassifiziert – je weniger, desto besser.
- Gruppe I: höchstens drei Prozent Wasseraufnahme (frostbeständig)
- Gruppe IIa: drei bis sechs Prozent Wasseraufnahme
- Gruppe IIb: sechs bis zehn Prozent Wasseraufnahme
- Gruppe III: mehr als zehn Prozent Wasseraufnahme
Was die Abriebsfestigkeit, Säurebeständigkeit oder Trittsicherheit angeht, geben wir auf Nachfrage gern genauere Tipps.